Фонд перспективных исследований: через 20 лет роботы смогут иметь чувствительную кожу
Руководитель лаборатории ФПИ Андрей Носов рассказал о проекте по разработке "нервной системы", которая будет контролировать состояние узлов и агрегатов авиационной техники
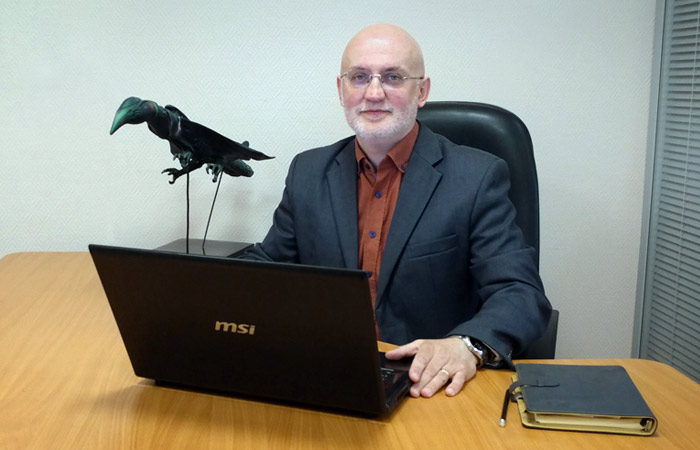
Москва. 29 мая. INTERFAX.RU - Фонд перспективных исследований (ФПИ) реализует проект по разработке "нервной системы", которая будет контролировать состояние узлов и агрегатов авиационной техники, а в будущем – и человекообразных роботов. О технологии, которую уже испытывают на перспективном скоростном вертолете, в интервью обозревателю "Интерфакса" Илье Морозову рассказал руководитель лаборатории ФПИ Андрей Носов.
- Андрей Анатольевич, как возникла идея создания такой системы?
- Начну с того, что наука вплотную подошла к вопросу "оживления" неживого. Поясню: речь идет о наделении технических устройств функциями, присущими живым организмам, в частности человеку. Уже появляются первые разработки, которые показывают перспективность этого пути. В дальнейшем подобные системы будут глубоко модифицироваться и развиваться по своему функционалу.
Мир вступает в новую эпоху, в которой человек всё больше исключается из управления машинами. Всё меньше и меньше требуется его постоянное участие в повседневной эксплуатации роботов. Человек становится гарантом последнего сигнала, принятия финального решения. Если говорить о боевых машинах, то речь идет о команде на уничтожение объекта или его сохранение, так как роботам запрещено принимать критические решения: "красная кнопка" остается в руках человека.
- В чем суть вашей разработки?
- Мы работаем над проектом по заказу Фонда перспективных исследований. Речь идет о разработке системы контроля за непредсказуемым поведением конструкций, работающих в жестких условиях, в которых возможно повреждающее воздействие на них: в боевой обстановке, при эксплуатации техники в арктических условиях и пр.
Для авиации, например, особенно важны гарантии безопасности и надежности, которые позволят сохранить экипаж в пилотируемой технике или дорогостоящий аппарат-беспилотник.
Такая система должна обладать несколькими ключевыми характеристиками и возможностями. Прежде всего, она должна быть автоматизированной, иметь механизм перепроверки данных для исключения ошибок и ложной тревоги, должна быть надежной в эксплуатации, служить долгие годы и гармонично работать не в ущерб основному предназначению конструкции.
- Как работает система?
- Мы сумели связать несколько разнородных физических принципов в единый технологический клубок. В композитный материал на стадии его изготовления укладывается по определенному принципу сеть оптоволоконных датчиков. Второй вариант – оптоволокно наклеивается на материал в нужных местах.
Толщина волокна 250 микрон. По сути это кварцевый провод, внутри которого лазером нанесен датчик. Световой пучок, распространяясь по волокну, сталкиваясь с оптическим преломлением, скажем так, с преградой в виде дифракционной решетки, часть света отражает. По отраженному сигналу мы и судим о физическом воздействии на этот датчик – преграду. При возникновении физической деформации решетка увеличивается в своих размерах и отраженный сигнал меняется.
Сеть датчиков через оптические разъемы подключена к бортовому блоку-регистратору, в котором находится источник излучения – широкополосный лазер. Сигнал попадает в фотоанализатор и переводится в цифровой, после чего информация идет в компьютер, где обрабатывается программой и записывается.
Наша конструкция может чувствовать силовое воздействие, по аналогии с тем, как человек чувствует прикосновение, удар, температурное воздействие. Для этого используются не только уже известные деформационные оптоволоконные датчики, но и разработанные нами акустические датчики, которые интегрированы в эту систему.
- Что дает акустический датчик?
- По аналогии с человеческим организмом, где по звуку сердца определяют правильность его работы, конструкция из композитного материала издает, скажем так, потрескивания. Контролируя "правильность" его звучания, мы можем узнавать о состоянии материала. Если звук в пределах нормы, все хорошо, если нет – мы должны это знать заранее, до разрушения конструкции. Причиной этого может быть что угодно – любое внештатное воздействие, начиная от случайных ударов и заканчивая ее повреждением.
- Почему вы используете аналогию с живыми организмами?
- Исходя из вышеназванных параметров, наиболее подходящим способом контроля состояния механизма является имитация систем организма человека. Нет ничего совершеннее биологического организма, находящегося на высокой стадии эволюционного развития, которым является человек.
Начиная разрабатывать и внедрять нашу технологию, мы ориентировались на необходимость следовать именно организму человека в качестве образца.
- На каком этапе сегодня находится разработка?
- Мы в рамках проекта Фонда перспективных исследований планомерно довели эту тему до уровня технологической готовности, в отношении которого уже сегодня принимаются решения о внедрении в образцы перспективной техники. Датчики и сенсоры, интегрированные в те или иные конструкции, которые могли осуществлять контроль по отдельным параметрам, существовали и ранее, а наша заслуга в том, что мы смогли вывести процесс этих "ощущений" механизмов на более высокий уровень, который свойственен не простейшим живым организмам, а существам с высоким уровнем развития.
- Проводятся ли испытания системы на авиатехнике?
- Сейчас одна из конфигураций нашей системы проходит летные испытания на перспективном скоростном вертолете (ПСВ) Московского вертолетного завода (МВЗ) имени Миля.
Мы будем продолжать искать новые функциональные возможности оптического волокна. Мы входим в святая святых – в объемный по своим параметрическим возможностям мир, где мы можем изучать ситуацию под разными углами и интерпретировать информацию, полученную с разных точек зрения. Возможность слышать и "чувствовать" выводит нашу конструкцию в разряд интеллектуальных систем нового поколения.
- Система может снабжать экипаж актуальной информацией в полете?
- В полете производится экспресс-анализ. Если нагрузка выходит за рамки установленного порога, блок автоматически дает сигнал пилоту, перед которым на панели управления загорается желтый или красный индикатор, в зависимости от степени проблемы.
- Сможет ли в будущем система не просто указывать на факт проблемы, а делать так, чтобы летчик точно знал: что и где повреждено у машины?
- Сегодня некоторые конструкторские бюро категорически против того, чтобы давать подробную информацию пилоту, так как он и так сильно перегружен. Сейчас система больше нужна для того, чтобы предсказать состояние самолета перед вылетом. Но, например, МВЗ видит нашу систему как вспомогательную для пилота, чтобы он понимал состояние вертолета и правильно оценивал возможность того или иного маневра, исходя из текущего положения. Вертолет сам по себе сильно вибрирует, иногда летчик может не успеть вовремя почувствовать усиление вибрации, причиной которой стала, допустим, трещина.
Система может очень многое: в зависимости от требований заказчика, мы можем варьировать объем выводимой экипажу информации.
- Как внедряется оптоволокно в композит?
- Если мы говорим об автоклавном методе производства, то берутся тонкие слои препрега – композитного полотна толщиной 0,2 миллиметра, пропитанного связующим, дальше они укладываются как слоеный пирог в нужной конфигурации, внутрь закладываются нити оптоволокна и затем все это запекается в автоклаве под давлением при определенной температуре.
- В современном самолетостроении композиты часто применяются?
- Например, на Ту-214 СМ из композитов изготовлена обшивка воздушного тормоза, а у МС-21 полностью композитные крылья. Там при производстве автоматически идет раскрой крыла, которое режет лазер.
- На некомпозитных материалах ваша система может применяться?
- Да. На перспективном скоростном вертолете мы установили систему сигнализации на невращающихся металлических элементах автомата перекоса. Как известно, лопасти вертолета, помимо вращательного движения осуществляют и вертикальные махи, этот процесс управляется металлическими тягами, на которые мы и наклеиваем датчики.
- Это дорого?
- Если учесть стоимость самой машины, сумма относительно небольшая.
- То есть, этими датчиками можно оборудовать уже эксплуатирующуюся технику?
- Да. Причем, в зависимости от требований заказчика, мы можем сделать и вариант проще, и сложнее. От этого будет зависеть и цена. Внедрение серийного производства также снизит стоимость.
- Каковы дальнейшие перспективы для развития этой разработки?
- Наша задача, чтобы лет через двадцать роботизированные устройства имели свою чувствительную "кожу". Самолет – тот же робот во многом. И сегодня наша система делает его внешний контур интеллектуальным.
Будущее в том, чтобы система сама принимала решения и подстраивалась под любые неожиданные изменения. Дальше мы будем продолжать усложнять ее, расширять ее функциональные возможности, наделяя бОльшим количеством свойств нервной системы живого организма.
- Если перейти в более практическую плоскость, кто интересуется этой системой?
- Это "Туполев", "Сухой", "Иркут", Московский вертолетный завод, "Камов". Группа компаний "Кронштадт", занимающаяся беспилотными аппаратами.
- У них есть интерес применять эту систему в серии?
- Используемые сегодня в авиастроении материалы в дальнейшем невозможны без применения системы контроля, который будет диагностировать и предупреждать внезапное развитие ситуаций, приводящих к разрушению того или иного элемента, что может привести к катастрофе.
Новые материалы обладают рядом уникальных свойств, которые недоступны тем же металлам, но сложность в том, что тот же композит может при определенных условиях внезапно потерять свои свойства.
У композита ряд свойств позволяет, скажем так, извлекать из минимума максимум. Это не просто пластик, это армированный пластик. При критической нагрузке металл разлетится на части, а композитное волокно превращается в тряпку. Он будет до последнего сохранять несущую способность, но при превышении предела он резко теряет это свойство. Если металлическое крыло под давлением критичного потока воздуха начинает, постепенно терять свою функцию, то композитное теряет ее внезапно.
- Этот момент можно просчитать?
- Нет, нельзя: у композита разброс свойств очень большой. Но можно вовремя заметить косвенные признаки грядущих проблем, что позволяет спрогнозировать возможное развитие ситуации.
Например, те же звуки, щелчки, которые издает композит во время своей деформации. Когда они становятся опасными, и мы видим, что связи внутри материала разрываются, мы можем понять, что датчики показывают нарастание деформации, хотя внешне это еще никак не проявилось. Мы видим и слышим, что организм "болен".
Именно в этом смысле важны внедренные нами акустические датчики, потому что по датчикам деформации нельзя вовремя понять о разрушении композита.
Сегодня проверка состояния композитного узла проводится людьми: самолет прилетел, подошел специалист с прибором ультразвукового контроля, проверил и дал заключение о дальнейшей возможности эксплуатации той или иной детали. Датчики нашей системы позволяют получить данные без привлечения человека: система выносит вердикт сама.
- В чем причина нестабильности характеристик композита?
- В основном, из-за особенностей изготовления. В зависимости от самой производственной площадки, от человека, который укладывает слои при изготовлении композита, получаются и разные характеристики.
- Если этот процесс автоматизировать, удастся повысить стабильность характеристик при производстве?
- Да, если укладывать слои будет робот.
- На каких-то самолетах есть уже внедренная в композит система контроля?
- Мы будем проводить стендовые испытания реальной вертолетной лопасти. Когда мы продемонстрируем результат работы системы: что она позволяет снимать данные даже с вращающейся лопасти вертолета и не влияет на нее негативно, производители задумаются о преимуществах интегрированных в конструкцию датчиков и возможности интеграции нашей системы.
Надеемся, что пошагово, с помощью диалога и научно-исследовательских работ, мы сможем выйти на новый уровень и проводить другие испытания интегрированных волокон.
- Какого результата вы ждете от массового внедрения системы в авиастроении?
- Это повышение безопасности полета, снижение стоимости эксплуатации за счет своевременного обнаружения проблем и снижения числа ошибок. Упрощение системы контроля за техникой с одновременным повышением его качества. По сути это иной метод проверки и контроля узлов и механизмов.