Глава инжиниринговой компании "ТопТех": нельзя пересесть с западной иглы на восточную, один раз уже обожглись
Алексей Поляков рассказал, как реализуются проекты после ухода ряда компаний с рынка
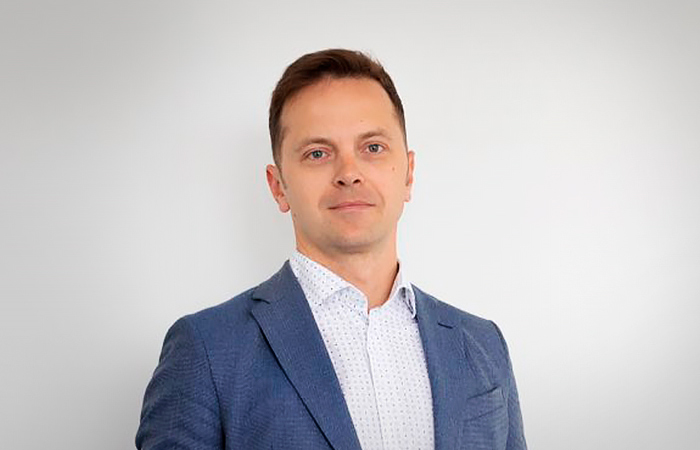
Москва. 15 мая. INTERFAX.RU - Уход с российского рынка иностранных инжиниринговых компаний поставил российский нефтегаз в затруднительное положение - отрасль осталась без компетентных подрядчиков, способных не только проектировать и реализовывать технически сложные проекты, но и без специалистов, которые могут обеспечить надежную эксплуатацию пущенных в работу установок. Кто занял нишу, где ранее главную партию играли западные игроки, рассказал "Интерфаксу" генеральный директор инжиниринговой компании "ТопТех" Алексей Поляков.
- На какой базе была создана ваша компания?
- "ТопТех" разрабатывает решения для нефтепереработки и химической промышленности, делая акцент на базовом проектировании, т.е. основе, которую раньше внедряли на российском рынке только иностранные компании.
В СССР существовало много проектных институтов, которые специализировались на определенных отраслях и занимались разработкой полного цикла технологий, оборудования и реализацией проектов. Позднее, после перестройки, уже в современной России всю эту нишу заняли иностранные компании, и наработанная ранее база проектирования и создания технологических решений исчезла.
Наша компания была создана в июле 2022 года. На тот момент в ее костяк вошли специалисты, инженерный состав московского офиса датской Topsoe, которая покинула российский рынок. Мы поняли, что для нас открываются новые возможности. Накопленные опыт и знания при реализации проектов по всему миру позволили нам создать инжиниринговый центр, центр компетенций, который востребован на российском рынке.
- Отрасль долгое время базировалась на международных корпоративных брендах. Не считаете ли вы, что сейчас пришло время для продолжения ее работы в "безымянном" формате? Или планируете продвигать свой бренд?
- Заказчики связывают реализацию проекта с компанией, которая может предоставить им надежное решение как в начале (спроектировать, разработать оборудование, обеспечить поставку, управление проектом, СМР), так и поддержать на дальнейших стадиях реализации: при пуске установки и техническом сопровождении ее работы. И мы себя позиционируем как единый центр ответственности. Наша компания дает заказчикам возможность получить полное сопровождение всей реализации проекта. Мы - не проектный институт, который заканчивает работу на проектной части и не поставщики оборудования, которые поступают аналогичным образом. И мы - не отдельная сервисная строительная компания, которая делает только свой объем работы. Мы осуществляем комплексное сопровождение от момента запуска и подготовки проекта, расчета финмоделей, технико-экономического обоснования до пуска и эксплуатации агрегатов и установок. "ТопТех" работает чуть меньше двух лет, но это уже довольно узнаваемая компания в отрасли, и мы наращиваем свое присутствие на рынке.
- Представители крупных компаний отрасли, например, "Газпрома" считают, что в настоящее время в инжиниринге не хватает системных интеграторов, которые бы понимали саму технологию заказчика, могли бы сформировать технические требования, сопроводить проект на всем этапе до внедрения, понимали бы вызовы отрасли. Вы согласны с таким утверждением?
- И да, и нет. Наша компания фокусируется на технологических решениях, где мы с одной стороны имеем большой опыт в расчетах оборудования, с другой - внедряем инновационные подходы при разработке технологических процессов. В мире нет ни одной компании, которая владеет абсолютно всеми технологическими решениями и способна закрыть все текущие потребности предприятий. Есть компании, которые специализируются на нефтехимии, на химических процессах, процессах нефтепереработки.
Наша деятельность включает несколько крупных направлений: получение синтез-газа, проектирование установок для получения водорода, метанола, аммиака. Отдельное направление - нефтепереработка: процессы гидроочистки и депарафинизации. Кроме того, уделяем внимание установкам гидрокрекинга, и это новое для российской отрасли направление, потому что раньше в России никто этим не занимался. Мы начали этот путь и сейчас активно его осваиваем, работаем с крупными заказчиками. Всю нишу занять невозможно, но накопленный опыт и знания в определенных областях позволяют нам предлагать современные решения всем крупным участникам рынка, среди которых "Газпром", "Газпром нефть", "НОВАТЭК", "Роснефть", "Фосагро", ГК "Азот", "Еврохим", "Уралхим", "Акрон" и другие.
- То есть специалисты в отрасли есть, но не все они способны предоставить комплекс услуг, которые требуются заказчикам?
- Все верно. Вопрос в подходе к организации работы. Мы в свою модель закладываем комбинацию мировых практик, когда подрядчик сопровождает проект полностью: с момента принятия инвестрешения или начала проектирования и до пуска с дальнейшим техническим сопровождением. У нас есть прекрасные проектные институты, которые обладают знаниями и компетенциями в проектировании специальных химических или нефтехимических процессов, но дальнейшая техподдержка и помощь при пуске не входит в их зону ответственности и работы. Здесь возникает разрыв, и это связано с тем, что в современной России все было отдано на откуп западным компаниям, которые предлагали сквозное технологическое сопровождение при реализации проекта. Мы сейчас выстраиваем всю эту цепочку.
- То есть, несмотря на изменившиеся условия, EPC-контракт, где подрядчик берет на себя обязательство передать заказчику уже построенный, готовый к эксплуатации объект, не требует трансформации, разбивки на отдельные спецуслуги?
- EPC-подряд очень удобен заказчику, когда он передает все риски при реализации проекта на компанию генподрядчика, и, тем самым, в какой-то мере страхуется, понимая стоимость, сроки и гарантии выполнения. Поэтому в любом случае эта модель будет востребована на российском рынке. Стоит отметить, что в разных отраслях сложилась своя специфическая практика. Так, в нефтепереработке многие проекты реализованы не по схеме EPC, а по схеме EP, где конкретно стройка и пусконаладка осуществлялись либо проектным офисом, либо проектной командой самих заводов. В крупных проектах химической отрасли, например, связанных с получением карбамида, где встроена целая цепочка процессов и объектов общезаводского хозяйства, как правило, привлекался зарубежный EPC-подрядчик для реализации под ключ.
Сейчас в российской химической отрасли мы сталкиваемся с тем, что 80% проектов реализует одна китайская компания - China National Chemical Engineering Co., Ltd. (CNCEC), в которую входят очень много проектных институтов и структур, занимающихся не только строительством, но и организацией поставок, сопровождением проектов. Им, тем не менее, просто необходимо привлечение российских проектных институтов, чтобы соответствовать нормам, правилам, требованиям прохождения наших госэкспертиз, стандартов промбезопасности. Мы, занимаясь разработкой базовых проектов, активно сотрудничаем с проектными институтами, которые на основе нашей документации делают рабочую документацию и переводят проект в стадию строительства.
- Подрядчик сейчас может гарантировать соблюдение бюджета и сроков? Или в настоящее время больше ответственности должен брать на себя заказчик?
- Заказчики обычно говорят, что всегда нужно чем быстрее, тем лучше, при этом с минимальными бюджетами и затратами. Мы называем реалистичные сроки исполнения договора. Все понимают, что при реализации любого проекта важна часть не только проектирования, но и этап поставки оборудования, сопровождение. Тесное взаимодействие с производителями оборудования, понимание потенциальных сроков производства и постоянный диалог с заказчиком помогают найти взаимоприемлемый вариант.
- Существует ли тенденция к концентрации инжиниринговых и строительных активов на стороне заказчика? Как в этих условиях независимому инжинирингу и управлению строительством оправдать свою уникальность и востребованность?
- Конечно, есть такая тенденция. Все крупные компании после 2022 года, а некоторые даже раньше, задумывались о своих инжиниринговых центрах или центрах компетенций, которые позволили бы им решать различные задачи, такие, как строительство новых производств, модернизация или реконструкция действующих объектов. Сейчас практически во всех крупных компаниях есть такие подразделения: в "Газпроме", "Газпром нефти", "ЛУКОЙЛе", "Акроне", "Еврохиме" и т.д. Эти специалисты обладают большим опытом эксплуатации установок, но, как правило, не владеют основами базового проектирования, проведения расчетов. Здесь наша роль выходит на первый план.
То же самое по сервису. Многие компании пытаются перейти на собственное обеспечение, отказавшись от технического сопровождения и сервиса. Но, например, перегрузка катализаторов аммиака происходит раз в 10 лет. Стоит ли компании развивать у себя этот функционал, если за 20 лет перегрузка катализаторов случится всего два раза? Тогда как мы работаем со многими компаниями, поэтому имеем постоянный опыт.
- Есть ли в настоящее время от нефтегаза какие-то уникальные запросы, с которыми вы ранее не сталкивались?
- Да, такие задачи есть, как правило, они связаны с разработкой комплексного решения, которое не всегда вписывается в наши основные направления деятельности. Например, мы проектируем агрегаты аммиака, а заказчику нужно целый комплекс построить - производство аммиачной селитры - и мы становимся ответственны не только за технологию получения аммиака, так как дальше нужно получить азотную кислоту, соединить ее с аммиаком и затем уже конечный продукт. Такие проекты - вызов для нас и расширение возможностей. Мы привлекаем партнерские компании и уже совместными усилиями обеспечиваем реализацию проекта. В текущих условиях приходится применять нетривиальные подходы, но в этом мы видим развитие и перспективу. Сейчас на российском рынке сложилась ситуация, в которой генподрядчики, которые могут реализовать крупные и средние проекты, уже сильно загружены на ближайшие несколько лет. И очень активно пытаются внедриться китайские компании. Наше преимущество в том, что у нас в портфеле есть решения, которые вообще никто не предлагает, например, автотермический риформинг для получения аммиака, метанола и водорода.
- Программой "обратного инжиниринга" в ТЭК поддержано 58 проектов на сумму более 3,5 млрд рублей, из них 33 проекта на сумму более 1,9 млрд руб. касаются нефтегазового машиностроения. Воспользовались ли вы этой господдержкой? Ваши проекты попали в этот список? С какими основными проблемами в обратном инжиниринге вы столкнулись?
- Мы пока не использовали программу Минпромторга по реинжинирингу, но имеем в портфеле два проекта, предполагающие условный обратный инжиниринг и поставку оборудования, которого нет на российском рынке. Однако это оборудование еще нужно разработать, а не только поставить. Мы понимаем, как это оборудование заместить, не сканируя его, просто обладая знаниями и компетенциями: делаем расчет, разрабатываем техпроект, подбираем варианты для его изготовления на мощностях российских предприятий. В качестве примера можно привести поставку тарелки для улавливания механических примесей в реакторе гидроочистки на Хабаровский НПЗ. Наши инженеры разработали технический проект, разработкой конструкторской документации и непосредственным изготовлением тарелки занималась российская компания "Стронг" на своих мощностях. По сути, это первый подобный опыт для российской нефтепереработки, небольшой, но знаковый проект с полной заменой иностранного оборудования российским.
При обратном инжиниринге основная проблема заключается в понимании возможностей российских машиностроительных предприятий и их техническом оснащении. По этому вопросу было плотное взаимодействие с производителями, анализ рынка и текущей ситуации. Например, производство оборудования для нефтепереработки и газохимии зачастую требует использования специальных высокотемпературных сталей. И тут есть две проблемы: эти виды стали не производятся в России, их завозят сюда, и при этом их обработка и вся работа с ними требуют особых навыков, с чем также имеются сложности. К счастью, многие предприятия сейчас наращивают и мощности, и производственную базу, чтобы соответствовать требованиям изготовления современного оборудования. И мы плотно взаимодействуем с производителями, потому что спроектировать оборудование можно - бумага все стерпит, а изготовить - уже может стать проблемой.
Если говорить о господдержке, то Минпромторг помогает налаживать взаимодействие между поставщиками технологических решений и заказчиками, выступая гарантом надежности предлагаемых подходов, минимизации рисков и привлечения финансирования на привлекательных условиях.
- В связи с последними внеплановыми ремонтами на нефтеперерабатывающих заводах увеличились ли к вам обращения со стороны нефтяных компаний по поводу оборудования или проектирования?
- Сейчас в российской нефтепереработке реализуются нескольких крупных проектов модернизации мощностей в рамках ранее заключенных инвестсоглашений с Минэнерго. Речь идет о вводе в ближайшие годы около 20 установок вторичной переработки нефти общей мощностью более 13 млн тонн в год. Поэтому мы с нефтепереработчиками на короткой ноге. Если говорить о внеплановых ремонтах, то здесь наша помощь, как правило, не требуется. Завод может сам все сделать, так как обычно речь идет о замене "железа", кабелей, трасс, где вся документация для этих установок уже разработана. То есть это просто поставка запасных частей, их монтаж и замена.
Например, поставленное ранее для одного из заводов "ЛУКОЙЛа" оборудование потребовало специальных запчастей для ремонта: включились российские предприятия, стали исследовать, кто данное оборудование может заменить и в какие сроки, это заняло время и сроки ремонта затянулись. А вот атмосферные и вакуумные колонны являются довольно простыми блоками, которые в России давно и проектируются, и производятся, и поставляются. Здесь вопрос только в оперативности работы заказчика и производителей этого оборудования.
- Как вы думаете, станет ли когда-нибудь возможным отказ от параллельного импорта, или такую задачу ставить нет необходимости?
- Это довольно сложный вопрос. Производственные мощности по выпуску оборудования и агрегатов для нефтепереработки, а тем более химии, в России ограничены по сравнению с теми же китайскими производителями, да и вообще с общемировым масштабом. Конечно, есть производители, которые с успехом реализуют импортозамещение или уже "импортоопережение" по разным направлениям. Однако есть точечные позиции, необходимые для двух-трех объектов, и требуют специального заказа. И когда приходишь с такой задачей к производителям, мы уже с этим столкнулись, и ведешь переговоры о том, что нужно провести научно-исследовательские разработки, тестирование, а это может занять год-полтора, то все расходы, как правило, будут помещены в первую стадию реализации проекта. Конкурентная способность производителя в таком случае в разы падает. Минпромторг поддерживает такие единичные заказы и пытается компенсировать подобные затраты, чтобы это не вырастало в какую-то несоразмерную сумму.
Мы не можем сейчас пересесть с западной иглы на восточную и продолжать полностью закупать оборудование. В этом нет логики: мы уже один раз обожглись, потом может быть второй - зачем этот риск? Сейчас и китайские, и индийские, и турецкие компании, и часть южно-европейских, которые позволяют себе работать с Россией, хотят поставлять оборудование и делать все возможное. Но, например, в России все установки в химической отрасли используют природный газ, а в Китае их можно сосчитать по пальцам с учетом того, что у них больше 400 агрегатов аммиака, а у нас кратно меньше. Крупные установки на природном газе они сами заказывают на Западе. В условиях богатых природных ресурсов газа в России переходить на китайские технологии в этой ситуации нелогично. Мы как раз активно работаем над созданием и выводом на рынок российских технологических решений для крупнотоннажных производств, которые позволят заказчикам получать продукцию, соответствующую всем международным стандартам.
- Вы также занимаетесь катализаторами. Какова текущая оценка рынка катализаторов ТЭК России: на сколько мы сами себя удовлетворяем и где по-прежнему зависим от сторонних поставщиков? Есть ли у вас от российских компаний конкретные запросы - какие катализаторы, с какими именно характеристиками им нужны?
- Ситуация на российском рынке катализаторов нефтепереработки выглядит довольно оптимистично: после первой волны санкций 2014 года многие компании активизировались и начали вести собственные разработки в этой области и организовывать производство. Мы оцениваем потребление катализаторов в российской нефтепереработке в 20-22 тыс. тонн в год. При этом потребность в катализаторах в некоторых направлениях, таких, как гидропроцессы, гидроочистка простых смесевых потоков, то есть гидроочистки дизеля, бензина, керосина в России, практически полностью закрыта российской продукцией. Сейчас все с нетерпением ждут пуска в эксплуатацию отечественного катализатора гидрокрекинга, так как до сих пор имеется 100%-ная зависимость от импортных поставок.
Помимо катализаторов гидрокрекинга завозятся и другие наиболее высокотехнологические и дорогостоящие катализаторы для процессов глубокой переработки нефтяного сырья (катализаторы депарафинизации, каталитического риформинга с непрерывной регенерацией и гидроочистки бензина каталитического крекинга), нефтехимии (катализаторы полимеризации - зависимость от импорта 90%) и производства водорода (почти 100%).
Есть позиции, потребление которых в России минимально и производить их просто нерентабельно, финансовые модели не работают. Развитие их производства целесообразно только с прицелом на экспорт, то есть нужно создать конкурентноспособный на мировом рынке продукт.
В то же время хорошим примером являются катализаторы гидроочистки - они меняются чуть ли не раз в год-два-три, у них цикл оборачиваемости довольно низкий, объемы большие - 3-4 тыс. тонн в год, имеется и экспортный потенциал.
В химической отрасли ситуация иная, по нашим оценкам, на сегодняшний день локализовано максимум 25% катализаторов, в основном для получения синтез-газа. Собственных проверенных катализаторов для синтеза метанола, аммиака, предриформинга в России на данный момент нет, а их разработка и вывод на рынок требуют длительное время. Специфика катализаторов газохимии определяется длительным средним сроком пробега одной партии (в среднем 4-5 лет в зависимости от типа катализатора), поэтому на данный момент можно говорить о том, что процесс перехода с западных катализаторов на их аналоги только начат, поскольку с момента ухода западных компаний с российского рынка прошло всего 2 года.
Если на установках водорода в России сейчас проводятся первые опыты внедрения отечественных катализаторов, то для выпуска аммиака и метанола катализаторов полного цикла в стране пока нет, к сожалению, но мы над этим активно работаем.
По ряду позиций еще встает вопрос экономической целесообразности. Например, катализатор аммиака - один из самых простых, но потребность в нем очень мала - в России это максимум 400-500 тонн в год. В то же время в Китае самый маленький производитель катализаторов аммиака выпускает 3,5 тыс. тонн в год, и таких изготовителей пять. Иными словами, один самый маленький производитель выдает уже в 10 раз больше, чем вся потребность российского рынка. А стоимость катализатора синтеза аммиака складывается в основном из затрат электроэнергии на его производство и на переработку руды, которая в Китае в основном и находится.
Со своей стороны мы участвуем в качестве технических консультантов в разработке катализаторов автотермического риформинга, новой для российского рынка технологии, которую мы активно продвигаем. Это довольно специфический и дорогостоящий катализатор, который требует тонкой настройки. Сейчас проводятся лабораторные испытания, скоро перейдем к пилотным. Параллельно участвуем в разработке катализатора вторичного риформинга, потребности в котором сейчас почти полностью закрываются импортом.
Кроме того, мы видим, что в России есть большая ниша потребностей химической отрасли в катализаторах, поэтому прорабатываем возможность создания собственного производства с привлечением партнеров.
- Правильно ли будет сказать, что у нас в стране не стоит задача полного импортозамещения катализаторного производства, и есть логика закупок в дружественных странах?
- Да, так и есть. И дело не только в том, что проще купить готовую продукцию, дело еще и в качестве. Если ранее на российском рынке присутствовало ограниченное количество производителей катализаторов, то сейчас рынок расширился, появилось много новых участников. Предприятиям приходится активно проводить пилотные испытания и сравнительный анализ предлагаемых катализаторов. За 2 года "ТопТех" обеспечил загрузку катализаторов разных типов на многие установки, большая часть поставок запланирована на осень. Для нас самих это важная составляющая работы, так как нам эти катализаторы нужны для расчета технологических процессов. Сейчас внутри "ТопТеха" мы активно следим за рынком катализаторов, оцениваем варианты собственного производства как катализаторов, так и оборудования на основании наших технических решений.
- В целом в инжиниринговом бизнесе кто является сейчас вашими основными конкурентами?
- Сложно выделить какого-то одного конкурента. Если говорить об аммиаке, то можно назвать ГИАП, который еще в советские времена активно разрабатывал свои технологии в этой области, однако утратил возможность реализации собственных проектов в современной России, занимаясь в основном адаптацией иностранных проектов без строительства своих установок. В нефтепереработке мы занимаемся настолько уникальными вещами, что вряд ли какие-то компании могут составить нам конкуренцию, разве что в массовых процессах, таких как гидроочистка светлых фракций. Наши знания и компетенции базируются на международном опыте и на оборудовании, которое мы разрабатываем, часть его уже запатентована.
- Есть ли у вас зарубежные проекты? Планируете выходить на внешний рынок?
- Мы уже работаем не только в России, но и в Беларуси, и в Сербии. Недавно осуществили поставку и загрузку катализаторов, проконтролировали пуск установок с получением кондиционного продукта. В России сейчас очень большой спрос, поэтому мы сконцентрированы на внутреннем рынке. Тем не менее, внешние предложения тоже рассматриваем, есть потенциальный интерес к участию в газохимическом проекте в Узбекистане.
- Что мешает вашему бизнесу? Какие вызовы перед ним стоят?
- Основной вызов - это кадровые ресурсы. Наша команда сейчас включает около 40 человек. Более половины из них - инженерный состав. Это ведущие эксперты с богатым опытом и уникальными компетенциями, которые занимались реализацией проектов по всему миру.
По мере роста деятельности мы привлекаем новых специалистов, точечно подбирая их для решения наших задач. Это трудоемкий процесс, поскольку для поддержания высокого уровня качества и сложности проектов у нас есть определенный уровень требований. Даже с учетом регулярного внутреннего обучения нам изначально необходимы кандидаты с серьезными профильными знаниями и хорошим уровнем понимания технологических процессов.
- Какие цели и задачи вы поставили себе на среднесрочную перспективу: доля рынка, объем выручки, портфель заказов, что-то еще?
- Наша основная цель - стать лидером российского рынка в разработке базовых решений для химической промышленности и нефтепереработки. Мы активно двигаемся к ее достижению - автоматизируем рабочие процессы, используем технологии искусственного интеллекта, минимизируя ручную обработку документов, ускоряем принятие решений. Например, сейчас во многих проектных институтах 80% времени уходит на подготовку документов, а не на расчет. Автоматизация этих процессов позволит нам перейти к полноценному использованию человеческого потенциала именно в инженерии, а не в рутинных делах.
Сейчас в российском инжиниринге нет явного лидера, каждая компания точечно закрывает свою нишу. И очень много китайских компаний, в сторону которых, прежде всего, смотрят предприятия при реализации новых проектов. И это главный вызов для нас.
Я бы так сказал: мы поймем, что стали лидерами, когда заказчики будут первым делом обращаться в нашу компанию за обсуждением внедрения наших технологических решений. Ну и в идеале, чтобы каждый второй проект в отрасли реализовывался бы на нашей базе. Мы не можем сказать, что должен быть каждый - это просто невозможно, но каждый второй - да, это амбициозно, но очень увлекательно.